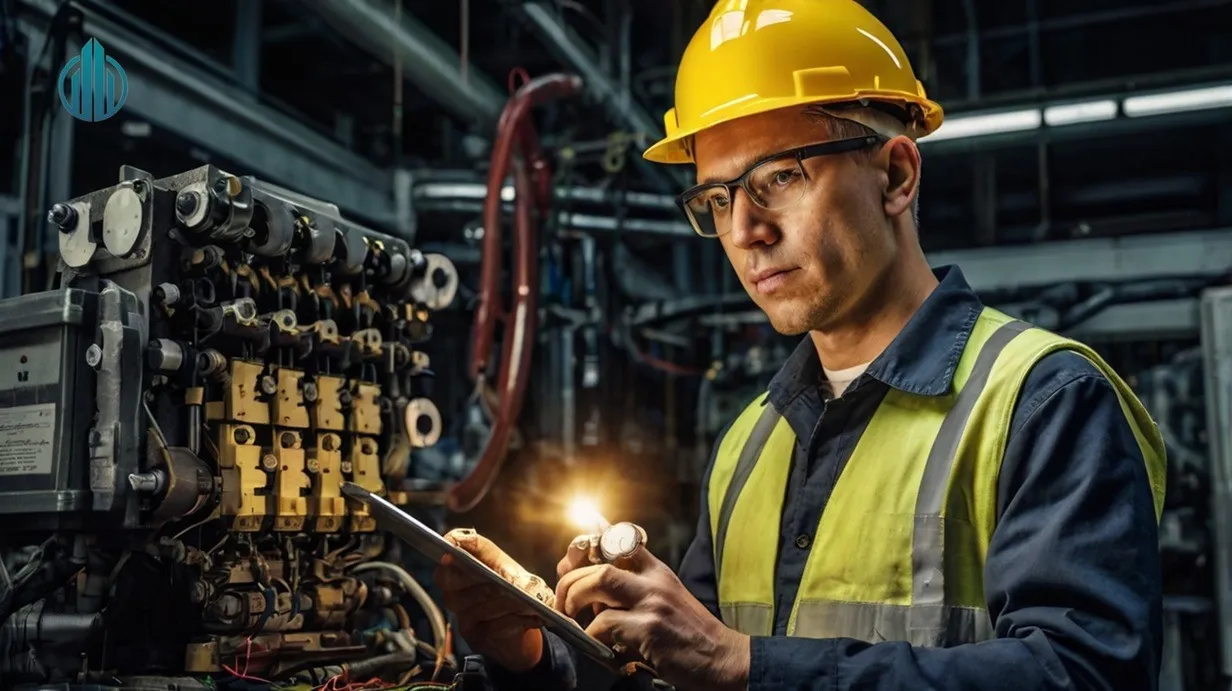
Keeping equipment running smoothly and avoiding costly breakdowns is a shared objective across industries. Yet, despite the common goal, many maintenance teams struggle to navigate the difference between preventive and predictive maintenance. Misunderstanding or misapplying these strategies can result in unnecessary costs, downtime, or reduced asset lifespan.
To address this, we will clearly define each approach, explore their differences, compare their pros and cons, and guide you on how to choose — or combine — them effectively using modern technology like CAFM system.
Defining the Terms: Laying the Foundation
What is Preventive Maintenance (PM)?
Preventive Maintenance (PM) refers to maintenance performed at scheduled intervals, regardless of the asset’s real-time condition. These intervals may be based on time (e.g., every month) or usage (e.g., every 1,000 hours or cycles).
Analogy: Much like changing your car’s oil every 5,000 kilometers — even if the oil still looks fine — PM assumes risk reduction through consistent care.
Goal: Minimize the likelihood of unexpected failures by sticking to a strict schedule of routine servicing.
What is Predictive Maintenance (PdM)?
Predictive Maintenance (PdM) is a more advanced strategy that uses real-time data from sensors and monitoring tools to determine when an asset is likely to fail — and acts just before that point.
Analogy: Imagine your car’s dashboard lighting up when your tire pressure drops or your engine temperature spikes — triggered by sensor data rather than time-based checks.
Goal: Optimize maintenance timing by intervening only when necessary, maximizing equipment life while avoiding sudden breakdowns.
Head-to-Head: Key Differences Between Predictive and Preventive Maintenance
This section will help you better understand predictive maintenance vs preventive maintenance and why choosing the right method matters.
Aspect | Preventive Maintenance (PM) | Predictive Maintenance (PdM) |
---|---|---|
Trigger | Based on schedule (time/usage) | Based on asset condition and data analysis |
Approach | Proactive, based on manufacturer guidelines | Proactive, based on real-time monitoring |
Data Requirements | Basic logs, usage tracking, manuals | Vibration, temperature, acoustic sensors, AI analytics |
Cost Profile | Low initial cost, potential long-term inefficiencies | High upfront investment, cost-effective in the long run |
Goal | Avoid failures by routine intervention | Predict failure to intervene at the optimal moment |
Weighing the Options: Pros and Cons of Each Strategy
Preventive Maintenance (PM): Pros
- Easier implementation with minimal technological requirements.
- Predictable budgeting due to fixed maintenance intervals.
- Effective for compliance-driven environments.
- Suitable for simple assets with well-known degradation patterns.
- Low upfront costs compared to PdM.
Preventive Maintenance (PM): Cons
- Over-maintenance risk: Replacing components that may still have useful life.
- Under-maintenance risk: Unplanned failures between intervals.
- Wasted resources: Labor and materials used unnecessarily.
- Inflexible: Cannot respond to unexpected wear or misuse.
Predictive Maintenance (PdM): Pros
- Minimized downtime through accurate failure predictions.
- Maximized asset utilization, replacing parts only when necessary.
- Improved safety, by identifying issues before they escalate.
- Optimized resource allocation, saving costs on labor and spares.
- Data-driven insights enhance decision-making and performance tracking.
Predictive Maintenance (PdM): Cons
- High initial investment in sensors, infrastructure, and data platforms.
- Requires expertise in data interpretation and system integration.
- Not ideal for all asset types, especially low-value or simple equipment.
- System reliability depends on data quality and analysis models.
Making the Choice: Which Strategy is Best for Which Assets?
Understanding the difference between preventive and predictive maintenance can help facility managers make more informed decisions.
Factors to Consider
- Asset Criticality: Is the asset essential for operations? PdM is preferable for mission-critical machines.
- Failure Impact: Will an unexpected failure incur high financial or safety risks?
- Failure Predictability: Is asset degradation measurable (PdM), or random (PM)?
- Cost-Benefit: Does the cost of PdM technology outweigh potential savings?
- Regulatory Compliance: Are there mandated PM intervals that must be followed?
General Guidelines
Use PM for:
- Non-critical or redundant equipment
- Assets with known wear patterns
- Assets under strict regulatory requirements
- Low-value machines where PdM doesn’t make economic sense
Use PdM for:
- Critical production machines
- High-value assets with significant downtime costs
- Equipment with measurable wear indicators
- Complex machinery where condition data can provide early warnings
The Best of Both Worlds: Combining Predictive and Preventive Maintenance
Rather than viewing it as predictive vs preventive maintenance, most organizations find success in combining the two.
Example: A manufacturing plant may use PdM for motors, bearings, and compressors while using standard PM schedules for air filters, lighting systems, and non-critical belts.
Flexibility is key. Tailor strategies by asset class, usage frequency, operational risk, and budget.
The Role of Technology: Enabling Smart Maintenance Strategies
Centralized Maintenance Hub
A robust Computer-Aided Facility Management (CAFM) system, such as CAFM IMS, brings both PM and PdM under one digital roof. It ensures:
- Accurate tracking of maintenance history.
- Automated scheduling of preventive tasks.
- Integration with IoT sensors and condition monitoring systems.
- Real-time alerts triggering predictive actions.
- Cost analysis and reporting to assess maintenance ROI.
Preventive Maintenance Automation
CAFM IMS allows managers to:
- Create custom time/usage-based schedules.
- Auto-generate work orders.
- Assign and track tasks across teams.
- Monitor compliance and service level agreements (SLAs).
Predictive Maintenance Integration
CAFM IMS can also:
- Integrate with vibration sensors, temperature monitors, or PLC systems.
- Trigger work orders when data anomalies are detected.
- Store and visualize condition data.
- Help correlate failures with asset conditions, enhancing future prediction models.
Key Takeaways & Summary
- Preventive Maintenance = Routine, schedule-driven care to prevent failure.
- Predictive Maintenance = Data-driven, condition-based strategy to forecast and avoid failure just in time.
- PM is simple and affordable, PdM is precise and efficient.
- The difference between preventive and predictive maintenance depends on asset value, failure risk, and operational impact.
- Combining predictive vs preventive maintenance approaches often yields optimal results.
- Technology like CAFM IMS empowers maintenance teams to execute both strategies seamlessly, improving uptime, compliance, and cost-efficiency.
Ready to implement a smarter maintenance strategy?
Contact Us and Discover how CAFM IMS supports both predictive maintenance and preventive maintenance.