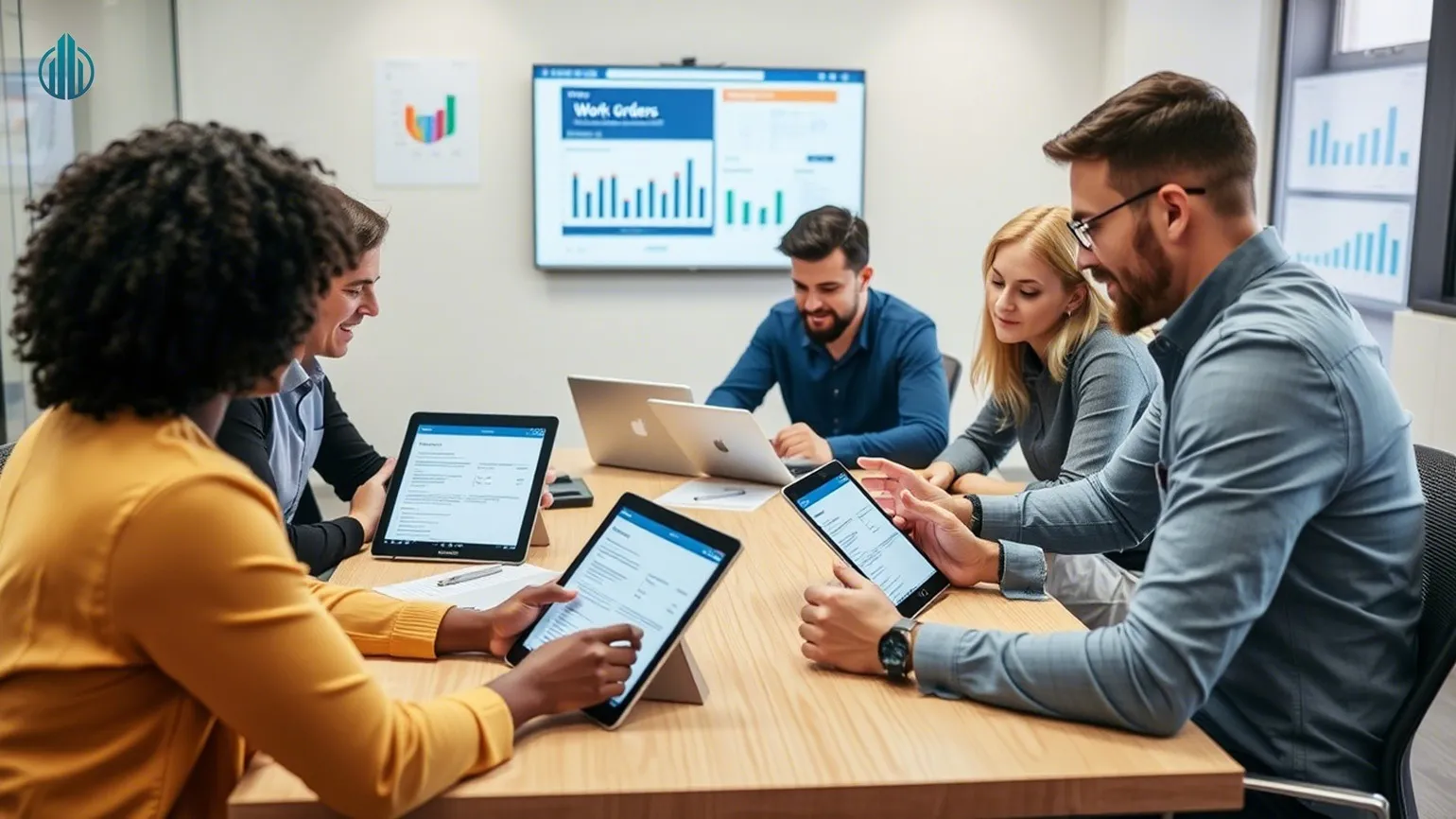
One minute you're fixing a critical leak, the next you're changing a lightbulb, and later you're setting up for a major client meeting. Facilities teams juggle an endless stream of tasks every day. Yet, treating all these activities as equal can result in chaos—inefficient scheduling, missed priorities, and unclear maintenance costs.
Categorizing work orders is a powerful strategy that facilities teams can use to bring structure and clarity to their daily operations. By managing work orders types, facility managers can streamline operations, enhance team productivity, and make smarter data-driven decisions.
This article defines the major maintenance work order categories, explains when and why they are triggered, and illustrates their real-world applications—all while emphasizing the critical importance of classification in facilities management.
Why Bother Categorizing Work Orders? The Benefits of Classification
Understanding and applying the right types of work orders can transform how a facility operates. Here's why:
- Accurate Prioritization
Not every task is equally urgent. A flickering hallway light can wait, but a burst water pipe cannot. Work order classification helps prioritize emergencies over routine maintenance. - Efficient Resource Allocation
Different tasks require different skills. By knowing the task type upfront, teams can assign the right personnel, tools, and time slots without guesswork. - Meaningful Reporting & Analysis
When work orders are tagged and classified, it’s easy to track how much time and money is spent on corrective vs. preventive tasks. This reveals where efficiencies can be gained. - Improved Budgeting & Forecasting
Analyzing maintenance work order categories over time allows better forecasting of costs, labor needs, and inventory management. - Clear Communication
With proper classification, both requesters and technicians understand exactly what the task involves, leading to fewer misunderstandings and delays.
Common Types of Work Orders Found in Facilities Management
Below are the key types of maintenance work orders used in modern facilities. Each plays a specific role in maintaining operational flow.
1. Preventive Maintenance (PM) Work Orders
Definition: These are scheduled tasks designed to prevent equipment failure and maintain optimal performance.
Triggers: Time-based schedules (weekly, monthly, annually), usage levels (runtime hours), or legal compliance requirements.
Goals: Extend asset life, reduce downtime, and ensure consistent performance.
Examples:
- Monthly air filter replacements in HVAC systems
- Quarterly lubrication of mechanical parts
- Annual fire extinguisher inspection
- Generator testing every 100 hours
2. Corrective Maintenance (CM) / Reactive Work Orders
Definition: Tasks initiated when an asset fails or malfunctions, requiring repair or replacement.
Triggers: Equipment breakdown, user complaint, or post-inspection fault detection.
Goals: Restore the asset to its normal operating condition quickly and efficiently.
Examples:
- Fixing a leaking faucet
- Replacing a burnt-out electric motor
- Repairing a malfunctioning elevator
- Adjusting HVAC settings after a system error
Note: If identified during inspection, it may be planned corrective; if sudden, it's unplanned/reactive.
3. Emergency Work Orders
Definition: Critical work orders triggered by immediate threats to safety, property, or operations. Require swift intervention.
Triggers: Fire alarm activation, chemical spills, security breaches, power failures.
Goals: Eliminate risk, protect people and assets, restore essential functions.
Examples:
- Repairing burst water pipes
- Resetting failed emergency lighting systems
- Fixing fire suppression malfunctions
- Responding to gas leak alarms
4. Inspection Work Orders
Definition: Non-intrusive evaluations to assess condition, performance, or safety.
Triggers: Routine compliance schedules, safety programs, or asset condition monitoring.
Goals: Identify problems before they escalate, ensure regulation compliance, and validate asset condition.
Examples:
- Daily building walk-throughs
- Weekly emergency exit checks
- Monthly lighting or signage inspections
- Biannual asset tagging and tracking audits
5. General / Service Request Work Orders
Definition: User-initiated requests that do not relate to maintenance or failure but support daily operations.
Triggers: Requests submitted through portals, phone calls, or emails from occupants or staff.
Goals: Enhance comfort, support events, or perform non-technical assistance.
Examples:
- Setting up chairs for a conference
- Moving desks or office equipment
- Hanging whiteboards or bulletin boards
- Helping with projector or AV setup
6. Predictive Maintenance (PdM) Work Orders
Definition: Advanced maintenance initiated by real-time data predicting likely failure.
Triggers: IoT sensors, condition-monitoring tools, predictive analytics platforms.
Goals: Minimize downtime, avoid unnecessary maintenance, and reduce costs.
Examples:
- Replacing a pump based on rising vibration metrics
- Adjusting equipment alignment from infrared imaging data
- Flushing systems due to abnormal fluid temperature
- Servicing motors before predicted failure thresholds
Putting it All Together: Using Work Order Types Effectively
Prioritization Framework
Not all work orders carry the same urgency. A structured hierarchy helps prioritize: Emergency > Corrective > Preventive > Inspection > General
Workflow Differences
Each type of work order can follow its own approval and scheduling pathway. For example:
- PM work orders may auto-generate based on schedules.
- CM work orders may need manager approval for spare parts.
- Emergency tasks can bypass formal steps for rapid action.
Reporting Insights
Tracking your maintenance work order categories over time offers deep insights:
- A high volume of CM work may indicate poor PM scheduling.
- Repeated emergency calls in the same area may reveal infrastructure weaknesses.
- Excessive general requests might show a need for better facility layout or resources.
How CAFM Software Simplifies Managing Different Work Order Types
Managing diverse work orders manually is inefficient. A Computer-Aided Facility Management (CAFM) system such as CAFM IMS transforms the process.
- Easy Categorization
Work order types are clearly defined and selectable at the creation stage, reducing confusion and improving accuracy. - Customizable Workflows
You can automate task routing, approval chains, and technician assignments depending on the work order type. - Filtered Views & Dashboards
Facility teams can filter by type, priority, or location to view only relevant tasks and generate focused reports. - Integrated Data
Work orders are linked to asset data, so each task—whether preventive or emergency—comes with full historical context, improving diagnostics and decisions.
Summary
Facility teams are responsible for a wide range of requests—from emergencies to inspections and service setups. Managing them under a single, undifferentiated process leads to inefficiencies and missed priorities.
To recap:
- Types of work orders include Preventive, Corrective, Emergency, Inspection, General, and Predictive.
- Proper classification enables prioritization, planning, reporting, and budgeting.
- Leveraging CAFM systems like CAFM IMS makes managing these categories seamless and powerful.
Is your current system struggling to manage the variety of tasks your facility handles?
See how CAFM IMS streamlines the entire work order management process, no matter the type. Visit Our Work Order Management Page
Request a demo to explore customizable work order types and workflows in CAFM IMS! Request a Demo Now