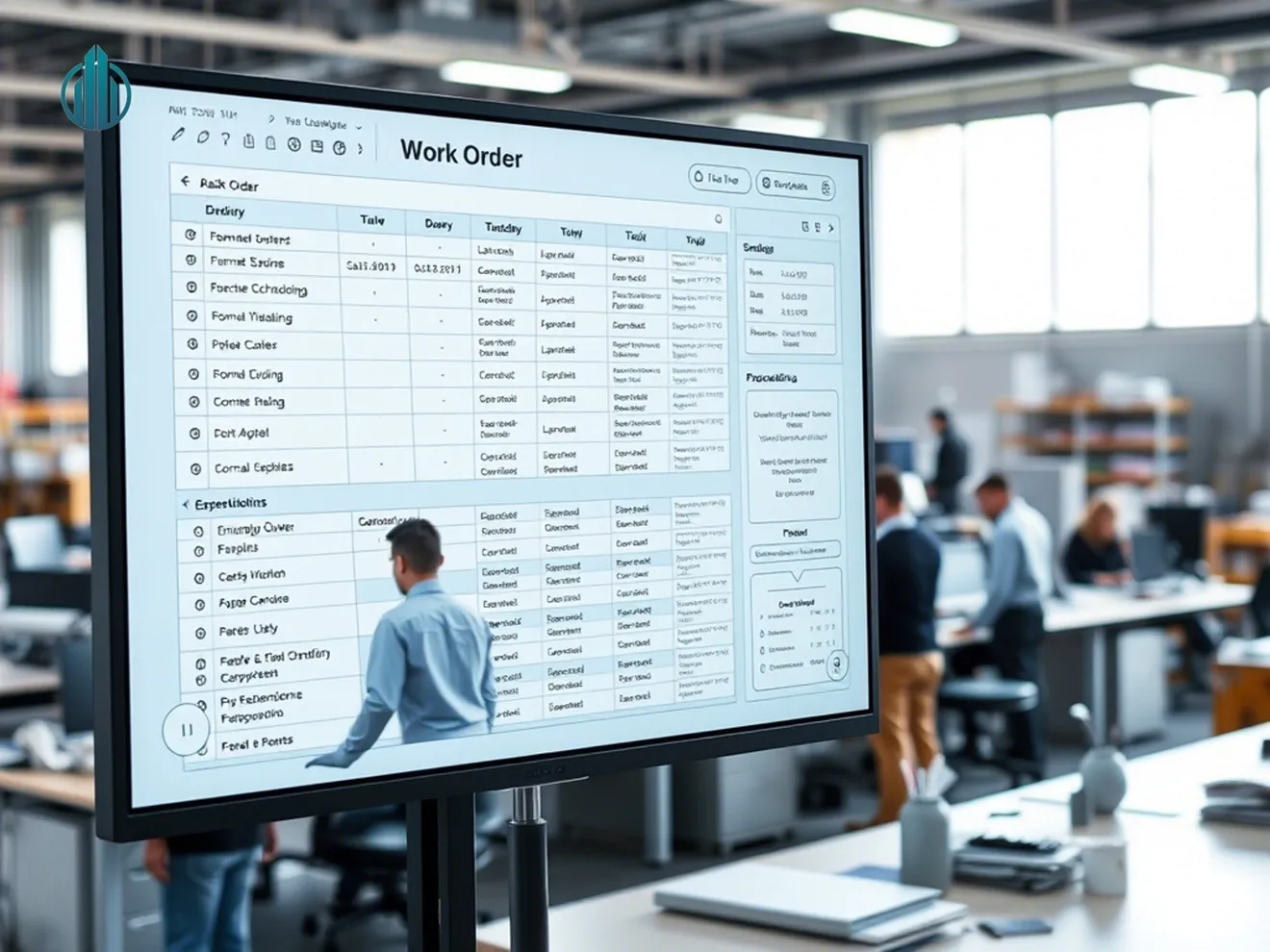
Imagine a maintenance technician walking through a facility with a coffee-stained notebook, a handful of sticky notes barely clinging to the wall, and a backlog of verbal complaints that no one remembers logging. An email about a broken HVAC system was lost in a cluttered inbox. A water leak reported last week still hasn’t been addressed. These small mishaps lead to delayed repairs, unhappy tenants, unsafe environments, and unnecessary costs.
Poorly managed maintenance isn’t just inefficient—it’s a liability. And the solution to this disarray is embracing work order management.
This article dives deep into what is work order management, explores what is a work order system, and highlights the undeniable benefits of a work order system that any facilities manager can’t afford to ignore.
What is Work Order Management? A Precise Definition
Work order management is the systematic process of creating, assigning, executing, and closing maintenance tasks, known as work orders, in a consistent and trackable way.
The primary goal is simple yet powerful: ensure maintenance is handled efficiently, transparently, and with full documentation from start to finish.
What is a Work Order?
A work order is a formal request for a task to be completed, usually related to repair, maintenance, or operational support. Common examples include:
- Fixing a broken light fixture
- Resolving HVAC malfunctions
- Conducting scheduled preventive maintenance
- Addressing safety hazards
- Preparing a facility for an event
Each of these needs a reliable process to ensure no detail slips through the cracks—which is exactly what a robust work order system provides.
The Lifecycle of a Work Order: From Request to Reporting
Understanding the stages of a work order lifecycle is essential to grasp how an efficient work order management system functions.
Stage 1: Request & Initiation
Work orders can originate from various sources: a tenant raising a concern, a routine inspection, or a scheduled preventive maintenance task. A reliable intake method (like a portal, app, or centralized form) ensures requests aren’t lost or forgotten.
Stage 2: Creation & Approval
Once initiated, the request becomes a work order by capturing crucial information:
- Location of the issue
- Related asset
- Detailed problem description
- Priority level
Some organizations may require approval based on budget or criticality before moving to the next step.
Stage 3: Scheduling & Assignment
Tasks are prioritized based on urgency, impact, or resource availability. The system assigns the work to the appropriate technician or team based on expertise, location, and availability. Scheduling ensures the work is planned and not left to chance.
Stage 4: Execution & Tracking
The technician carries out the task, ideally using a mobile application to:
- Mark progress
- Record time spent
- Note parts or tools used
- Update task status in real time
This is where the benefits of a work order system really shine—through transparency, accountability, and real-time data capture.
Stage 5: Completion & Closure
After verifying that the work is successfully completed, the order is formally closed in the system. Final notes, costs, and resolutions are logged for future reference.
Stage 6: Reporting & Analysis
Completed work orders are a goldmine of data. Facilities managers can:
- Identify maintenance trends
- Measure technician performance
- Forecast asset replacements
- Optimize preventive strategies
Why Work Order Management is Vital for Every Facility
Improved Efficiency & Productivity
A streamlined work order management system reduces:
- Time spent chasing incomplete tasks
- Confusion over who is responsible
- Duplicate work
- Bottlenecks in approvals
Tasks move faster. People stay accountable. Nothing slips through the cracks.
Substantial Cost Savings
Timely repairs reduce the risk of asset failure and emergency repairs. Having full visibility on labor and parts usage ensures budget compliance. Historical cost data justifies preventive maintenance investments and highlights inefficient assets.
Enhanced Communication & Collaboration
Centralizing work requests and updates in one platform improves communication between staff, technicians, and management. Everyone knows what’s happening—when, where, and by whom.
Greater Accountability & Performance Tracking
Every action is logged: who completed the task, how long it took, what was used. This builds a reliable performance history for individuals and teams and supports better decision-making on future workload distribution.
Better Asset Management
Work order histories provide insights into asset performance. Managers can identify recurring issues, decide when to replace equipment, and design more effective maintenance schedules.
Improved Safety and Compliance
High-priority and safety-related tasks are flagged and resolved promptly. Comprehensive logs ensure that inspections, repairs, and compliance checks are all documented and accessible—crucial for audits and legal protection.
Why Spreadsheets and Sticky Notes Fall Short
Manual methods like paper forms, email trails, and spreadsheets simply can’t keep up. They:
- Don’t scale
- Get lost or duplicated
- Offer zero real-time updates
- Make reporting time-consuming
- Lead to costly errors
How Work Order Management Software Elevates Operations
Dedicated work order management software—like the one included in CAFM IMS—transforms maintenance processes.
- Centralized Control: All work orders, from initiation to closure, live in one accessible platform.
- Automation: Set automated alerts for overdue tasks, route work orders to the right teams, and trigger preventive maintenance schedules—no manual follow-up needed.
- Mobile Accessibility: Field technicians use mobile apps to receive tasks, update statuses, and record time and materials on the go.
- Real-Time Visibility: Dashboards provide real-time insights into open, in-progress, and completed tasks. Management can instantly see where bottlenecks are forming.
- Advanced Reporting: Generate insightful reports to evaluate KPIs, cost trends, technician performance, and asset reliability—without touching a spreadsheet.
- Seamless Integration: A true work order system connects with inventory, assets, purchasing, and preventive maintenance modules—creating a 360-degree view of your facility operations. CAFM IMS excels in this integration, empowering facilities to run smarter and leaner.
Key Takeaways
- What is work order management? It’s the structured, traceable handling of maintenance tasks from request to reporting.
- What is a work order management system? A digital platform that facilitates the full lifecycle of maintenance work with efficiency and accuracy.
- The benefits of a work order system are vast—better productivity, cost savings, communication, compliance, and asset longevity.
An effective work order system isn’t just a nice-to-have; it’s the foundation of operational excellence in facility management.
Streamline Your Maintenance with CAFM IMS
Ready to streamline your maintenance workflows and gain control over your facility operations?
👉 Discover how the CAFM IMS Work Orders Management module provides the tools you need for efficient task tracking and completion