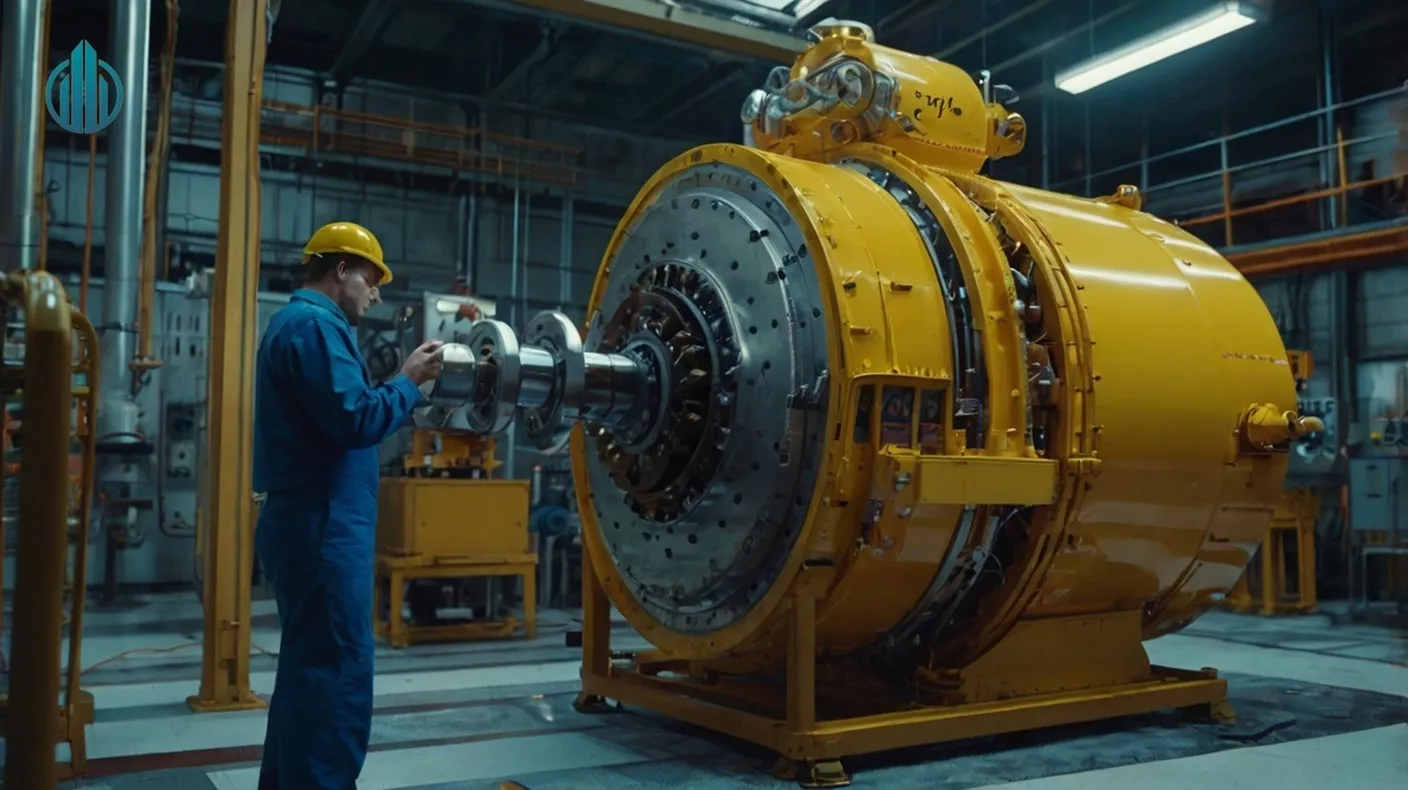
Imagine this: a key production line goes down due to an unexpected motor failure. Emergency repairs are expensive, and downtime costs spiral. On the flip side, you’ve been replacing components based strictly on time-based schedules—many of which still had useful life left. Sound familiar?
This is where Predictive Maintenance (PdM) enters the scene—a smarter, data-driven strategy that prevents failures and eliminates waste. Instead of reacting to breakdowns or over-maintaining equipment, PdM helps you intervene just before something goes wrong.
In this article, you’ll discover what predictive maintenance is, the technologies behind it, its benefits, how it compares to other maintenance approaches, and how you can start implementing it in your operation.
What Exactly is Predictive Maintenance (PdM)?
Predictive Maintenance (PdM) is a maintenance strategy that uses real-time data, sensors, and analytics to monitor the actual condition of equipment. It detects potential failures and performance issues before they lead to downtime.
Unlike preventive maintenance, which relies on time or usage intervals, PdM responds to the actual health of the asset. This means less unnecessary maintenance and far fewer surprises.
The core goal? Maintain equipment at the right time—not too early, not too late.
The Technology Behind the Prediction: How Does PdM Actually Work?
Step 1: Condition Monitoring & Data Collection
PdM begins with monitoring equipment performance using specialized technologies. These include:
- Vibration Analysis – Ideal for motors, pumps, and rotating machinery.
- Infrared Thermography – Detects abnormal heat patterns indicating electrical or mechanical issues.
- Oil Analysis – Reveals internal wear or contamination in lubricated systems.
- Ultrasonic Testing – Identifies compressed air leaks, steam traps, and electrical faults.
- IoT Sensors – Monitor parameters like temperature, pressure, humidity, and energy usage in real-time.
All these tools help build a comprehensive picture of asset health.
Step 2: Data Analysis & Pattern Recognition
Data from sensors is only valuable when analyzed correctly. This is where Machine Learning (ML), Artificial Intelligence (AI), and advanced statistical techniques come in.
These systems:
- Analyze data streams to detect anomalies
- Establish what “normal” performance looks like
- Alert you when equipment deviates from those baselines
Step 3: Predictive Modeling & Failure Forecasting
Once patterns are understood, predictive models estimate when a failure is likely to occur. This includes calculating:
- Remaining Useful Life (RUL)
- Probability of Failure
- Impact of Performance Degradation
Step 4: Actionable Insights & Maintenance Triggers
The end goal isn’t just to predict—it’s to act. PdM systems convert insights into:
- Maintenance recommendations
- Automated work orders
- Urgency levels based on severity
This enables teams to act only when needed, with maximum efficiency.
Predictive vs. Preventive vs. Reactive Maintenance: Understanding the Differences
Reactive Maintenance (Run-to-Failure)
- Trigger: Equipment fails
- Pros: Zero planning, low up-front cost
- Cons: High repair costs, unplanned downtime, safety risks
Preventive Maintenance (Scheduled)
- Trigger: Calendar or usage meter
- Pros: Reduces risk of failure, predictable
- Cons: May cause over-maintenance, ignores real-time condition
Predictive Maintenance (Condition-Based)
- Trigger: Asset performance data
- Pros: Timely interventions, minimal downtime, optimal cost
- Cons: Requires investment in sensors, analytics, and skilled personnel
Key takeaway: Predictive Maintenance is the most efficient model, offering the best ROI through strategic, timely interventions.
The Compelling Benefits of Implementing Predictive Maintenance
- Drastically Reduced Unplanned Downtime
Identify and address potential failures before they stop operations. - Optimized Maintenance Costs
Avoid unnecessary work while cutting emergency repairs. - Extended Asset Lifespan
Maintain based on true need, not guesswork. - Improved Safety
Catch hazards before they escalate into incidents. - Efficient Resource Scheduling
Align parts and labor with actual maintenance needs.
Getting Started: Key Considerations for Implementing PdM
- Identify Critical Assets
Start with equipment where failure means major disruption. - Understand Failure Modes
Know how your assets typically fail to select the right sensors and monitoring strategy. - Select & Implement Monitoring Technology
Choose technologies that match failure detection needs. - Establish Data Infrastructure
Plan how to collect, store, and manage sensor data securely. - Choose an Analysis Platform
Use a facility managment platform (like CAFM IMS) that can process data and generate predictions. - Develop or Use Predictive Models
Whether custom-built or pre-configured, models are essential for forecasting. - Integrate with Your Maintenance Workflow
Your PdM insights must connect to a work order system for seamless execution. CAFM IMS supports this. - Train Your Team
Ensure your team can interpret data and act on it quickly.
The Role of CAFM in Your Predictive Maintenance Strategy
CAFM IMS: Your PdM Enabler
- Data Hub: Centralizes maintenance records, asset data, and sensor inputs.
- Workflow Automation: Converts PdM alerts into automatic work orders.
- Holistic Management: View condition-based insights alongside preventive tasks and cost analysis.
- Reporting Tools: Visualize trends, anomalies, and risks via intuitive dashboards.
CAFM IMS doesn’t just support PdM—it amplifies it.
Summary
- Predictive Maintenance uses real-time data and analytics to forecast asset failure.
- It goes beyond preventive and reactive approaches for better uptime, lower costs, and improved asset longevity.
- Successful PdM demands proper tools, data infrastructure, and integration into systems like CAFM IMS.
Ready to harness the power of data for smarter maintenance?
Explore how CAFM IMS supports advanced maintenance strategies, including integration points for predictive maintenance solutions.
Talk to our experts about building a more proactive maintenance program with CAFM IMS. Book a Demo