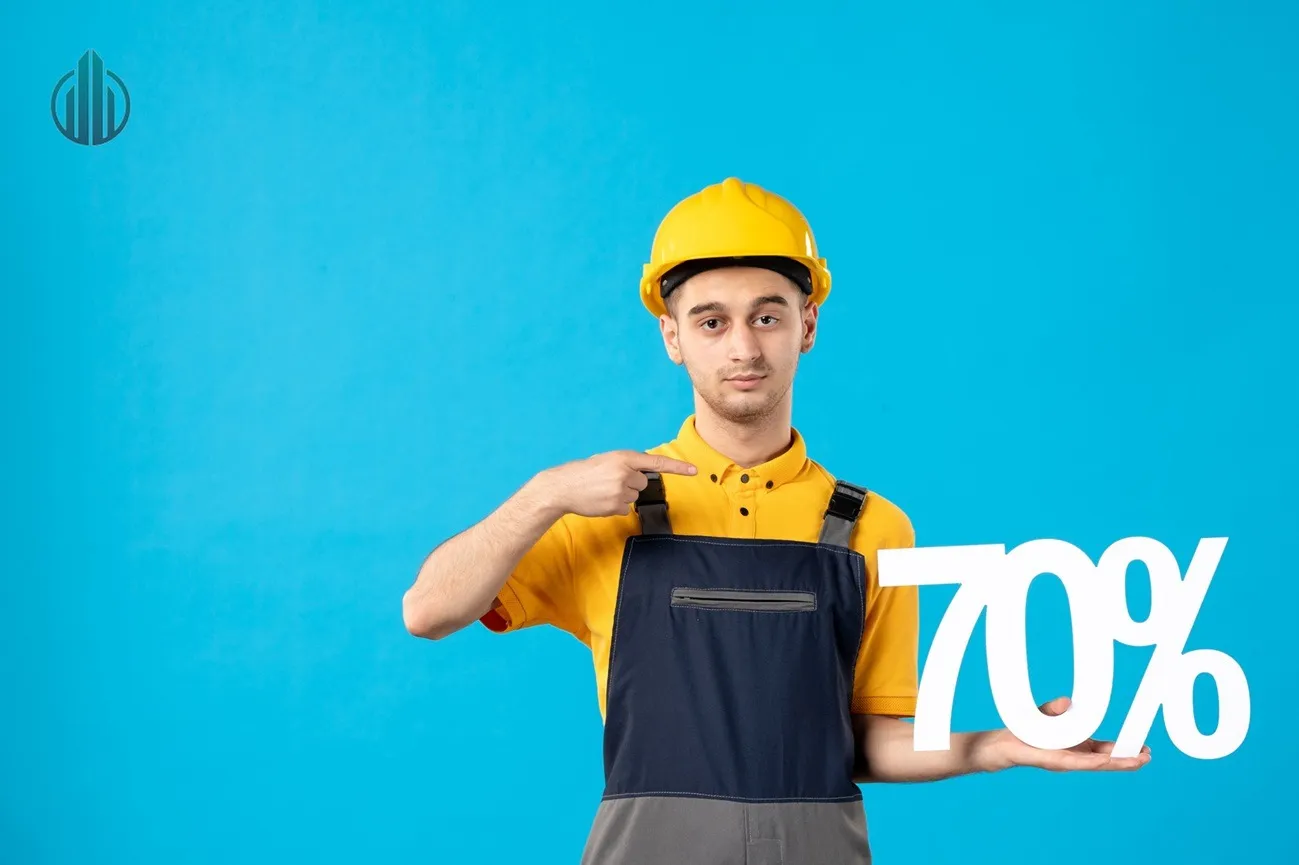
Maintenance is crucial for keeping equipment, buildings, and assets in good working condition. When maintenance is neglected, breakdowns become inevitable, leading to costly repairs, unplanned downtime, and safety hazards.
Preventive maintenance (PM) is a proactive approach designed to prevent failures before they occur. Instead of waiting for things to break down, PM ensures that equipment and systems are regularly inspected, serviced, and repaired as needed.
In this article, we’ll explore what preventive maintenance is, its types, benefits, and how to implement an effective preventive maintenance program.
What is Preventive Maintenance?
Preventive maintenance (PM) is a structured maintenance strategy that involves regularly scheduled inspections, servicing, and repairs to prevent unexpected failures.
Goals of Preventive Maintenance:
- Reduce the risk of sudden equipment failure.
- Improve asset lifespan.
- Reduce maintenance costs over time.
- Ensure operational efficiency.
- Enhance workplace safety.
A preventive maintenance solution helps businesses minimize costly downtime and maintain smooth operations.
Types of Preventive Maintenance
Preventive maintenance can be categorized into several types based on how maintenance schedules are determined:
1. Time-Based Maintenance
Time-based preventive maintenance follows a fixed schedule, such as servicing machinery every six months, regardless of its usage. This method is ideal for assets with predictable wear and tear.
2. Usage-Based Maintenance
Usage-based maintenance is triggered when an asset reaches a specific usage threshold, such as every 1,000 hours of operation or every 10,000 production cycles. This approach ensures maintenance is performed when it's actually needed.
3. Predictive Maintenance
Predictive maintenance uses real-time data and analytics to predict when maintenance is required. Sensors, AI, and machine learning monitor asset conditions and trigger maintenance only when necessary—making it one of the most cost-effective strategies.
The Benefits of Implementing Preventive Maintenance
An effective preventive maintenance program provides numerous benefits, including:
1. Reduced Equipment Downtime
PM helps identify and address potential issues before they escalate into failures, significantly reducing unexpected breakdowns and downtime.
2. Maximized Cost Savings
While reactive maintenance (fixing broken equipment) is expensive, PM reduces repair costs and extends asset lifespan, leading to significant cost savings.
3. Increased Asset Lifespan
Routine maintenance prevents excessive wear and tear, ensuring equipment and facilities last longer and perform optimally.
4. Improved Workplace Safety
Regular maintenance prevents hazardous failures, reducing safety risks for employees and ensuring compliance with safety regulations.
Steps to Implement a Preventive Maintenance Program
Implementing an effective PM program involves the following steps:
1. Identify Key Assets
Determine which equipment and systems are critical to operations and require preventive maintenance.
2. Set Up PM Schedules
Establish maintenance schedules based on time, usage, or predictive analytics to prevent failures before they occur.
3. Automate Alerts and Notifications
Utilizing a Computer-Aided Facility Management (CAFM) system can streamline PM tasks by automating maintenance alerts and tracking work orders.
4. Track and Adjust Maintenance Plans
Regularly review maintenance data to adjust schedules, optimize resource allocation, and improve efficiency.
Conclusion
Preventive maintenance is essential for reducing unexpected failures, minimizing costs, and improving operational efficiency. By implementing a structured PM program, businesses can extend asset lifespans, enhance workplace safety, and improve productivity.
Don’t Hesitate:
Want to simplify preventive maintenance? Our CAFM IMS software includes features to help you set schedules, automate alerts, and track maintenance with ease. Explore our system today!
FAQs
1. What is a preventive maintenance program?
A preventive maintenance program is a structured plan that schedules routine maintenance to prevent equipment failures, reduce downtime, and improve efficiency.
2. What are preventive maintenance procedures?
Preventive maintenance procedures include inspection, lubrication, adjustments, repairs, and part replacements based on a scheduled plan to maintain equipment health.
3. How often should preventive maintenance be performed?
The frequency depends on asset type, usage, and manufacturer recommendations—ranging from daily inspections to annual overhauls.
4. What industries benefit the most from preventive maintenance?
Industries such as manufacturing, healthcare, facilities management, and logistics rely heavily on PM to ensure uninterrupted operations.
5. How can technology improve preventive maintenance?
Technologies like CAFM IMS software, IoT sensors, and AI-driven analytics optimize PM by automating scheduling, detecting faults early, and reducing manual work.